HV INSPECT
The challenge of preventing a defective device from being implanted in a patient.
The manufacture of coronary valve stents is a complex, multi-stage process involving the most advanced materials and state-of-the-art technologies.
However, the monitoring of the results obtained in the different stages of the manufacturing process, the quality control and the final inspection of these devices are carried out “manually” by experienced operators using classical Non Destructive Testing (NDT) techniques such as visual inspection, eddy current or liquid penetrant testing.
With this approach, control and inspection processes are time-consuming, costly and often represent the main bottleneck in the manufacturing process.
In addition, even if operators have experienced knowledge, manual inspections are unreliable because it is very difficult to avoid human errors that can lead to incorrect acceptance of a defective device.
HV INSPECT offers an advanced inspection technology solution for the coronary valve manufacturing process, which means increased accuracy, speed, reliability and traceability for inspection processes.
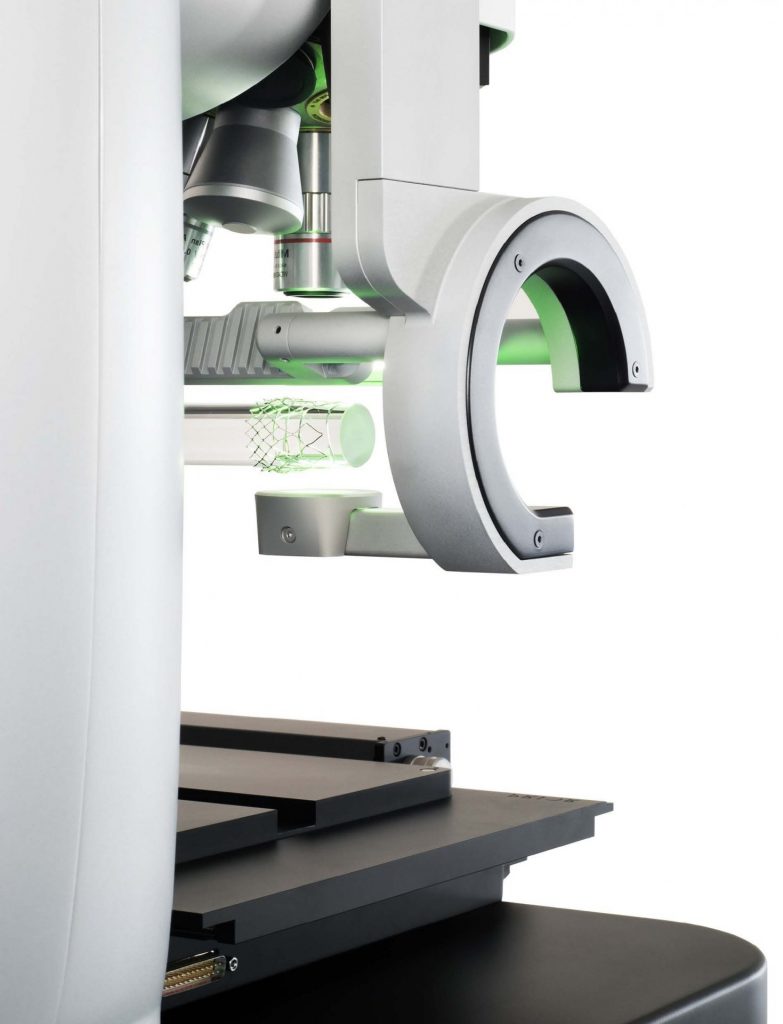
HV INSPECT is an industrial research project based on optical sensors, which allows the monitoring and automation of the manufacturing process of the new sutureless and transcatheter aortic coronary valves (TAVIs). This solution can be used both in the production process and in the final stage of on-line inspection and quality control. There is currently a widespread demand from vascular medical device manufacturers for more advanced inspection technologies. A technology that should bring accuracy, speed, reliability and traceability to the inspection process.
The HV INSPECT project study is oriented to the inspection of coronary valves of large peripheral stents. The developed prototype provides high-resolution and perfectly focused images of the outer and inner surfaces of the stent struts and also of their lateral faces. From these images, the analysis software simultaneously and automatically performs the pre-programmed measurement of critical device dimensions, as well as the detection and classification of imperfections according to the guidelines of a marked defect library.
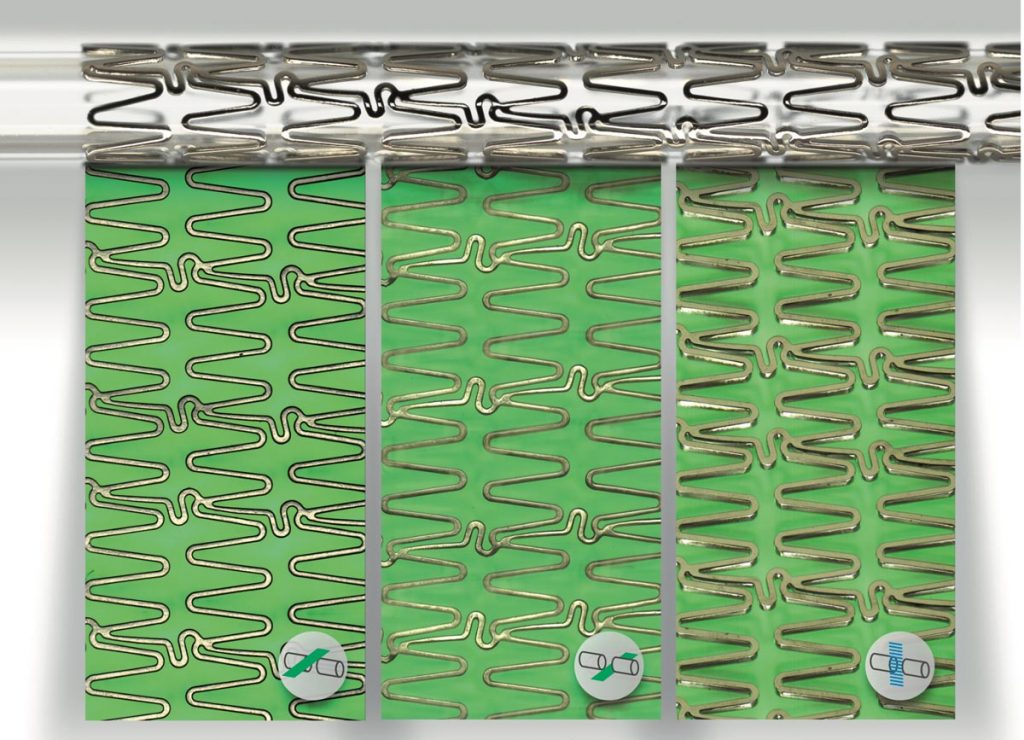
The “Q six” has been selected as the inspection system in a multinational project that will build the first fully automated medical device factory.
As a result of the AEI 2018 HV INSPECT project, a new Sensofar Medical product has been developed: the “Q six”, a platform configurable according to the application, following the Industry 4.0 orientation of the HV INSPECT project, which was presented at a trade fair in Japan in February 2020 and is also featured in the magazine Light! special health that secpho published in February 2020 (page 64). Sensofar Medical has also confirmed that the “Q six” has been selected as the inspection system in a multinational project to build the first fully automated medical device factory. The project aims to manufacture up to 4 million units per year of a device that will be made to serve for the prevention and treatment of aneurysms.